AnxinCel® Cellulose ether HPMC/MHEC products can improve Machine applied plasters through the following advantages: Increase longer open time. Improve work performance, non-stick trowel. Increase the resistance to sagging and moisture.
Cellulose ether for Machine applied plasters
Gypsum based and gypsum-lime based machine spray plasters are mixed and applied in continuously working plastering machines. They are used for a highly efficient coating of walls and ceilings and applied in one layer (ca. 10 mm thick).
Not all mortars are suitable for spraying with mortar spraying machines. The mortar that can not be sprayed by a machine is suitable for mechanized spraying. What mechanized spraying needs is special mortar, that is, "machine sprayed mortar".
Many times, people think that mortar can be sprayed out by a machine and can be applied to the wall. My mortar can be called "machine-blasted mortar." Whether the cost of equipment and consumables corresponding to the sprayed mortar is reasonable and the proportion of the mortar on the wall, whether there is rebound and sagging during the mortar spraying process, and more importantly, whether the dry mortar is suitable for high-rise dry powder transportation and other factors.
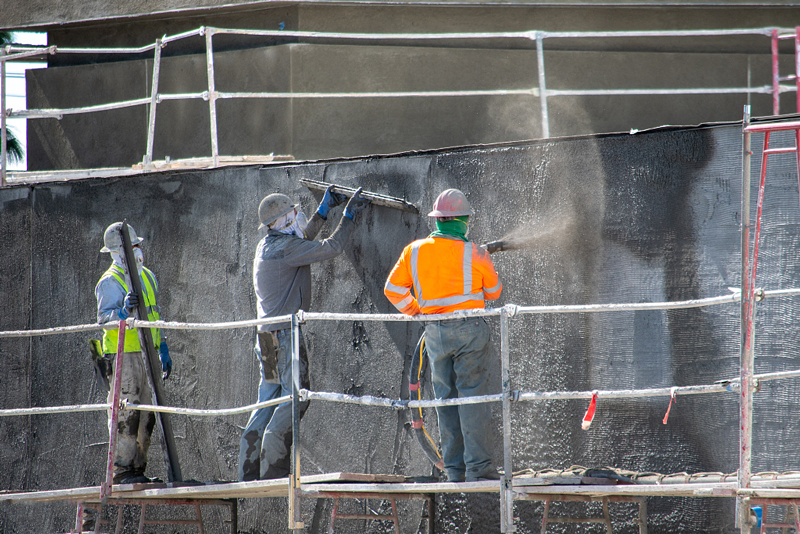
Only when the above-mentioned requirements are met can it be called "machine-blasted mortar".
The air washing steps of the mortar spraying machine:
Step 1: The pipeline should be equipped with a stop valve, and a stop plate should be inserted to prevent the concrete in the vertical or upwardly inclined pipe from flowing back.
Step 2: Take out some of the concrete at the mouth of the front straight pipe and connect it to the air-washing joint. The joint should be filled with a sponge ball soaked in water in advance, and the inlet, exhaust valve and compressed air hose should be installed on the joint.
Step3: Install a safety cover at the end of the pipe to prevent the concrete spray from hurting people.
Step 4: Slowly open the compressed air intake valve, so that the compressed air will press out the sponge ball and concrete. If the pipeline is equipped with a stop valve, it should be opened at the open position before opening the air valve.
Step 5: When all the concrete in the pipeline has been emptied and the sponge ball has been shot out immediately, the air washing is completed.
Step 6: Close the compressed air intake valve and start to disassemble various pipe fittings.
Recommend Grade: | Request TDS |
HPMC AK100M | Click here |
HPMC AK150M | Click here |
HPMC AK200M | Click here |